Quality Control Practices
Monitor
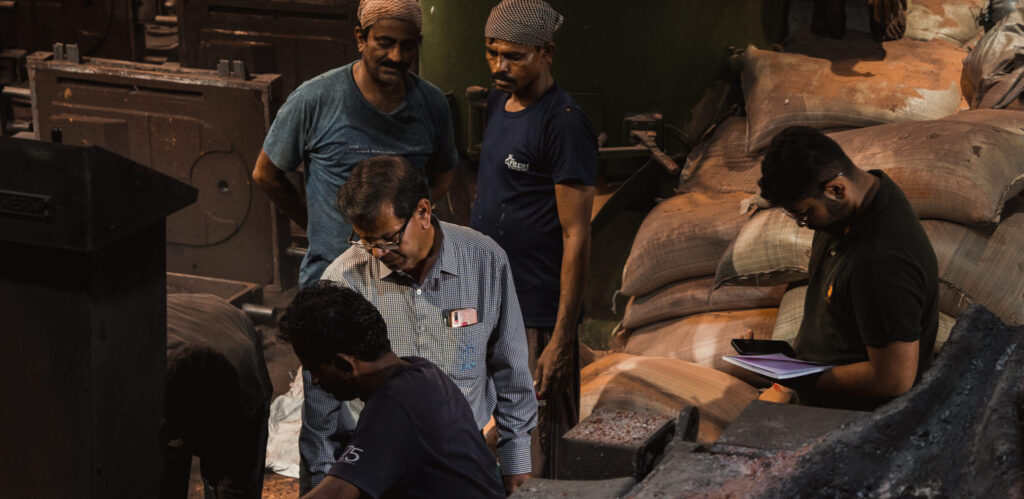
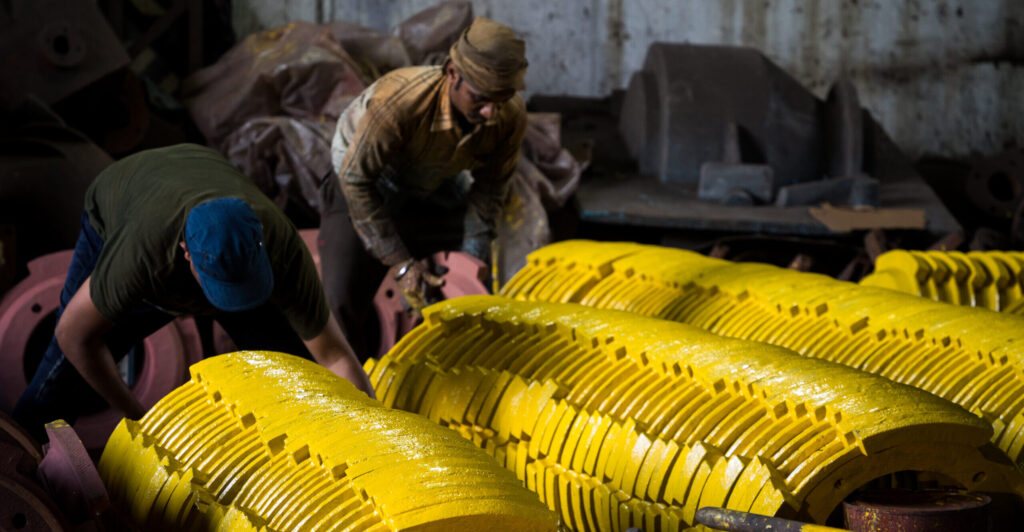
Sand Preparation
Sand preparation is a very important step of the moulding process as it is one of the initial processes and even a small error can result in the product being completely discarded.
Our team monitors sand preparation very keenly and leaves no room for errors. But we still make the sand go through quality inspection after preparation to ensure no room for error is left.
MOULD PREPARATION
METAL PREPARATION
Metal preparation and metal melting are one of the most important processes as it determines the quality of the metal.
Our team monitors every aspect of this process to its finest details using the latest available tools to make sure that exact figures are achieved for the metal prepared.
POURING TECHNIQUE
Different pouring techniques are used for different kinds of products. And it plays an important role in determining the quality and grade of the product.
We monitor our pouring process manually, to ensure no room is left for any error.
AeSTHETIC INSPECTION
Aesthetic errors are not just about the looks but also cause problems with the functionality of the product and hence no errors are allowed at this stage.
MEASUREMENT ANALYSIS
Any product being manufactured at our facility has a very specific purpose for our client and a small error in measurement can turn the product into a complete waste. Hence measurements are very important for our products.
We make sure to leave no scope for even a minor detail when it comes to the measurement of any product. And our accurate modern tools help us achieve the level of accuracy that we want from our products.
FINAL OBSERVATION
After our product has been through detailed monitoring at every stay of production we perform one more final inspection to ensure that only error-free products roll out from our facility.
inspection
A thorough inspection is carried out at every step of the manufacturing process to ensure we don’t miss any irregularities in the product.
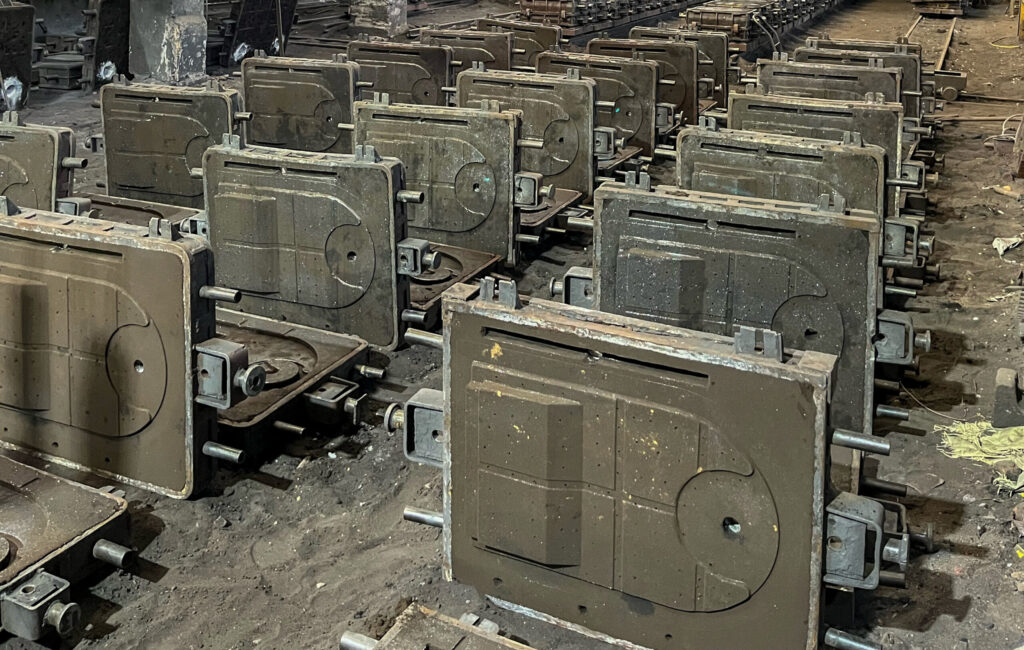
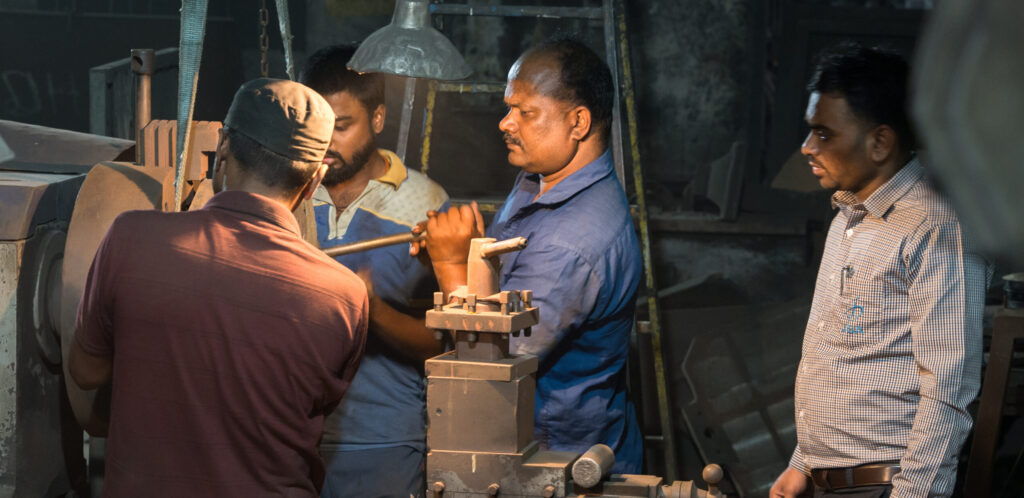
MOULD INSPECTION
We carry out a thorough inspection of every single mould made before it is used.
This helps us to guarantee that the mould meets our expected standards and quality requirements.
Every aspect from the dimensions to the quality of the mould is tested before being used for further process.
METAL INSPECTION
Metal quality is important in every step of our process. Starting right from the raw material quality to the alloys and finally product metal quality.
To ensure that we don’t leave any scope for error, we keep a close check on our metals at every step. And our latest tools find and eliminate the smallest of errors in our metal compositions or quality.
QUALITY INSPECTION
Quality is our buzzword and we don’t compromise on it for any reason.
To make sure we maintain our quality standard with every single product that we make, we impose strict quality inspections at every step of our production.
Our expert faculty and latest tools make our quality check accurate and reliable.
GRINDING INSPECTION
Grinding is part of our final stage finishing and hence requires a thorough inspection.
Our inspection team with the help of proper tools, check the accuracy and finishing quality after the product goes through the grinding process.
FINISHING INSPECTION
When the product has been through the complete manufacturing process and reached the final completion, it goes through a final finishing inspection.
The finishing quality of our products is important for their aesthetic and quality integrity.
No minor errors are allowed to pass through our final inspection.
testing
All our products go through a series of quality testing to make it to our clients. We carry out these testing with our latest tasting tools and machinery at our facility.
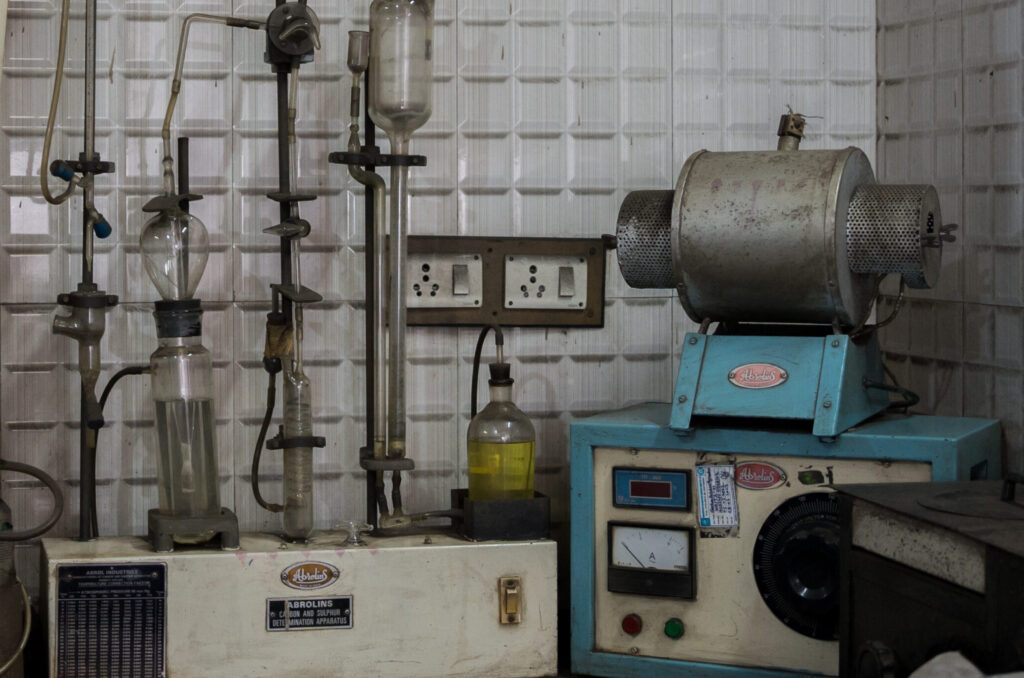
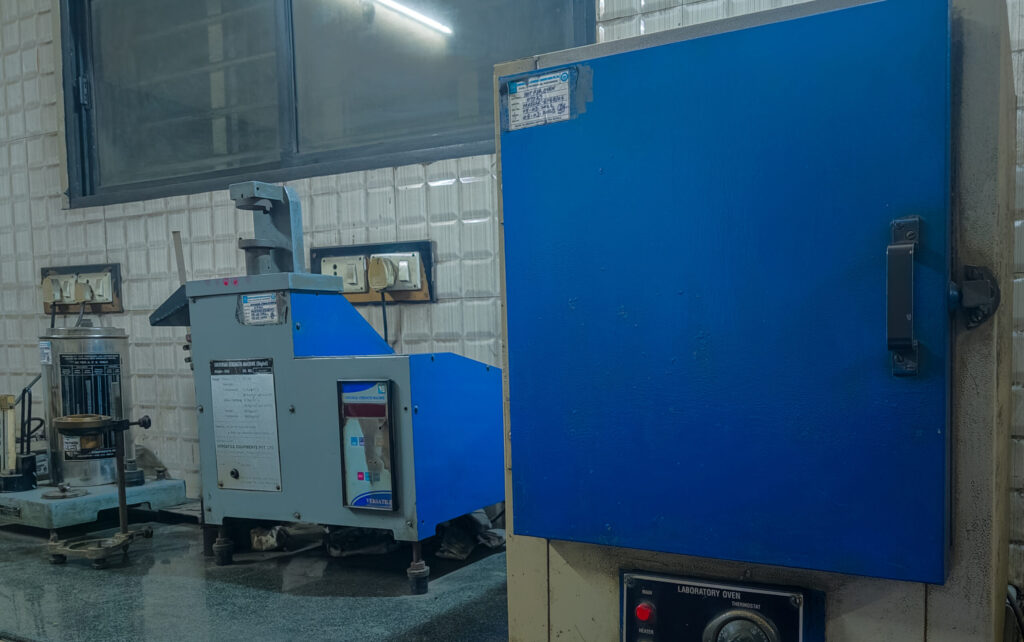
Brinell HARDNESS TESTING MACHINE
The Brinell hardness tester uses the oldest method of hardness testing commonly used today.
The brinell hardness testing machine allows almost all metals to be tested by way of the Brinell test.
This ensures that the correct hardness for the product is achieved.
CE METER FOR INSTANT CARBON SILICON ANALYSIS
It is a microprocessor-based carbon silicon analyzer series designed for molten cast iron analysis.
It consists of special electronic hardware & software which automatically correct errors introduced due to the derating/ageing effect of electronic components, ensuring long-term accuracy of measurements.
This helps in testing if the correct composition of alloy is achieved.
DIGITAL PYROMETER FOR MOLTEN METAL TESTING
A digital pyrometer is used to check the surface temperature of the molten metal and alloys.
It is used to check if the metal/alloy has reached the proper required temperature for further processing.
This helps us maintain the consistency and quality of the alloys before processing or casting.
PERMEABILITY TESTING MACHINE
This machine is used to test the permeability of raw sand, green sand and no-bake sand with digital calculations and readouts.
This is to determine the correct quality and state for the sand to be used for the casting.
This helps our team to ensure the sand and cast meet the exact required standards.
VOLATILE MEASURING MACHINE
A volatile measuring machine is used to determine the air quality and composition of any unwanted gases in the air.
Air quality and composition don’t he foundry can directly affect the workers and product quality.
Our team keeps a close check on this to avoid any damage caused by the air quality and keep the product quality in check.
DIMENSION CHECKING TOOLS
We use various types of callipers, scales and gauges to ensure that the perfect dimensions are achieved for the product.
We check and correct errors even minor details to make sure that we achieve the exact required dimension and quality for the product.